Fundamental Keys on Basic Instrumentation
- InviNP
- May 22, 2020
- 3 min read
This InviNP article/blog covers process control instrumentation. We will start in detail with a short introduction of the key concepts and terms used in process control. After this module you should understand, why instrumentation plays such a key role in modern process control both in terms of safety and quality and also the impact that these instruments have on operational costs.
we will present the most commonly measured process variables such as pressure temperature and flow. Finally, we will also show that the design of modern instruments makes them capable of measuring multiple variables and therefore knowledge of their operating principles plays an increasingly important role in designing new projects a process is broadly defined as an operation that uses resources to transform inputs into outputs. a typical example is an oil refinery where crude oil is transformed through a series of steps into gasoline the example shown here is a summary of how a process in a plant is organized a process can be split into three interconnected layers.
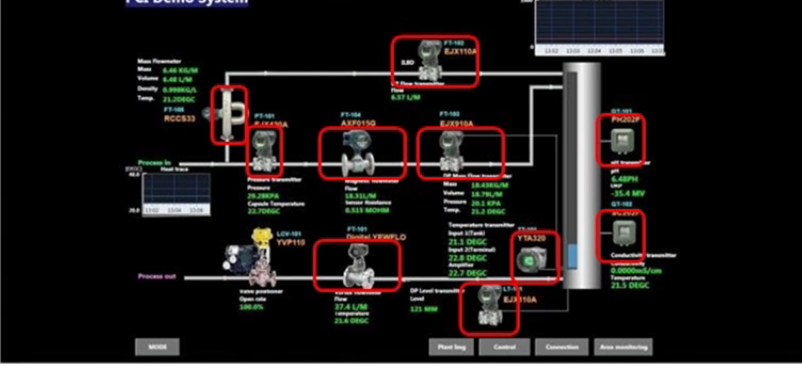
The first layer consists of the sensors and transducers commonly referred to as 'process instrumentation' these instruments measure the variables of interest at each step of the process.
the second layer is made up of the final control elements typically 'control valves' these instruments use the outputs from the sensors to adjust the process as needed. Incidentally, this diagram is of a real installation called a demonstration loop. the real flow loop will be shown later.
In this topic, it is important to understand the relationship between these three layers as they are in constant communication with each other this constant exchange of messages and information ensures that the users get the best results out of their process.
In every process, there are certain objectives that are required a process must be designed and operated to be safe at all times to constantly produce the desired amounts of high-quality products and last but not least to remain profitable... this is a difficult balance that requires good engineering practices at the design stage, when such practice is selecting a measuring process instrument that is safe to use in a given process as accurate and reliable as possible and able to maximize ROI.
It is also important that the instrument be selected according to the process variable it will be measuring and the application requirements sometimes. These guidelines are not followed sufficiently which can result in catastrophic consequences. there are many variables than can be measured during a process including
temperature,
pressure,
flow,
density,
level,
pH and conductivity...
These variables form the core of every industrial process additionally some applications call for the measurement of more specific variables such as concentration viscosity and turbidity.
However, the first seven variables are the most commonly measured.

This is the flow rig that was once used to illustrate the process layers. as previously stated, when instrument can measure several variables for example a Coriolis flow meter can measure both mass flow and density at the same time while a differential pressure transmitter can measure both the pressure and the flow.

This is another way of visualizing the different process layers with the control system on the right communicating with a different instruments on the left.
In the middle, you can see various protocols used to allow communication between the control room and the instruments including HART Foundation FIELD BUS, ISA 100 Wireless standard and PROFIBUS.
The choice of the particular protocol much like the choice of a measuring instrument is determined with the various application.
For more information or to contact us please visit our website
Comments